最先端技術を活用、卸の枠を越えて=PALTAC/RDC埼玉
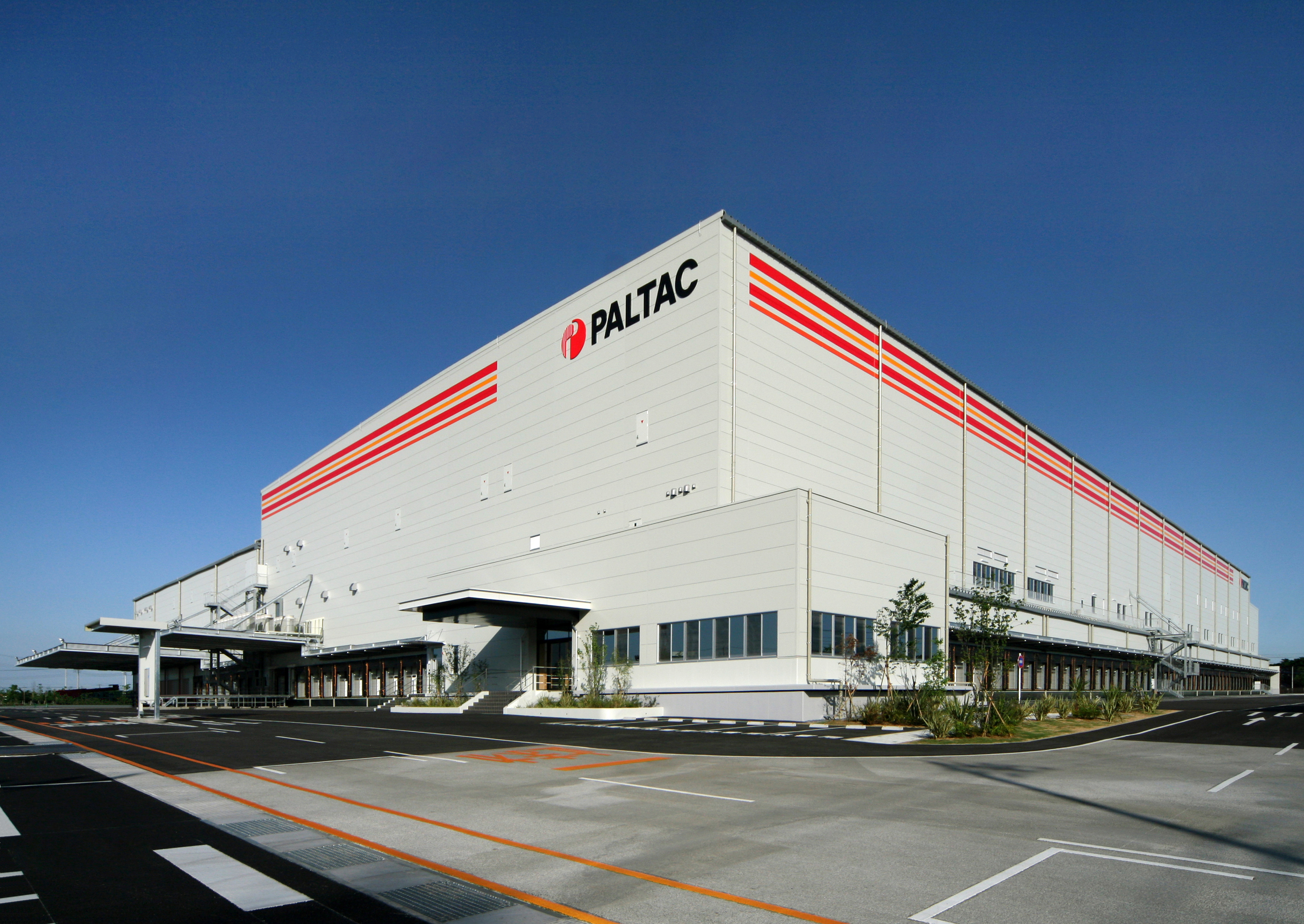
PALTAC(本社・大阪市中央区、糟谷誠一社長)が2019年11月に稼働した「RDC埼玉」(埼玉県杉戸町、写真)はAIやロボットなどの最新技術と、長年培った現場運営ノウハウを融合させた次世代型の大規模最先端物流センターだ。同社は卸売業でありながらも、センター設計については、社内に人材を確保し、自社で行っている。自前のWMSはもとより、「RDC埼玉」では物流の世界において“世界初”や“日本初”となる試みにも挑戦。とくに、「自動入荷検品システム」や、ティーチレスでピースピッキングをこなす「AIピースピッキングロボット」は物流センター業務の生産性を大幅に改善する画期的な取り組みとなっており、実際に同社の従来型のセンターとの比較では、人員生産性2倍をすでに達成しているという。
人手不足背景に持続的な物流システムの構築へ
「RDC埼玉」は敷地面積6万6620㎡、延床面積4万5475㎡の3階建て。用地と倉庫、および庫内設備を含めた総投資額は230億円に上る。RDCはRegional Distribution Center(大型物流センター)の略称で、全国16ヵ所に所在。RDC埼玉は千葉県浦安市で運用していた「RDC東京」を移転・拡張した拠点となる。
「RDCはこれまでもソーターやEDIの導入などで自動化していたが、それでも作業の中心は人手によるものだった」と三木田雅和・常務執行役員研究開発本部長は振り返る。一方で少子高齢化に伴う労働人口の減少を背景に、全国で作業員不足が確実に深刻化していく中、「生活に欠かせない商品を扱う当社が担っている社会的役割という視点からも、安心・安全かつ安定的に商品供給できる物流システムを構築する必要があった」という。
そこで、15年ごろから自動化・省人化を実現する新たなコンセプトの物流センター構想に着手し、最新のテクノロジーと同社の物流ノウハウを融合させた独自の次世代型物流システム「SPAID」を開発。まずは18年に開設した「RDC新潟」で運用し、同所で経験を積んだ上で、5倍の規模となるRDC埼玉の稼働に至った。
SPAIDの大きな特徴は、PALTACの事業特性でもあるバラ物流への対応だ。化粧品や日用雑貨、ヘルスケア関連商材を中心に約1000社のメーカーから商品を預かり、400社近くの小売企業へ卸す同社。取扱アイテム数は全国で5万SKU、RDC1拠点でも約2万SKUに上る。
従来のRDCでは作業員がカート台車を押しながら庫内を歩いてピッキングしてきたが、SPAIDでは人に代わって機械が商品を作業者の手前まで搬送してくる「MUPPS」システムを考案。これにより、RDC埼玉は全体生産性を従来の2倍――すなわち、同じ物量の出荷作業に必要となる人員数を従来の半分に抑えることに成功した。併せて、作業員の高齢化を想定し、手作業であっても「人にやさしい」仕組みとした。
佐塚大介・営業本部物流担当副本部長は「RDC埼玉では、人口減という課題への解決と高い作業品質を両立させ、『商品を必ず届け続ける』という安定性を実現した」と話す。
世界初の自動入荷検品システムで待機時間を3分の1に
具体的な庫内作業としては、まず入荷時に2つの自社開発のシステムを導入している。ひとつ目が「入荷予約システム」。これまではドライバーが “早い者勝ちで”バースに接車していたが、荷量と入荷時間を事前に申請し、バースを予約することで入荷待機時間を削減した。自社開発のWMSとも連動し、最適化している。
もうひとつが、世界初となる「自動入荷検品システム」だ。パレット単位で入荷される商品をコンベアに流すだけで、レーン搬送中にセンサーが自動的に品目とケース数を計数し、検品作業が完了する。これによりトラックの接車時間をさらに減らし、計数ミスも防止。2つのシステムで納品トラックの待機時間を3分の1に短縮した。
自動検品後の商品は自動搬送台車「ロボストレージ」によってパレット自動倉庫の最適な場所へ格納される。この時も、自動倉庫の特定レーンに入庫を集中させないことで生産性を高めるなど、運用の細部に渡って効率化を追求している。
ケース品の出荷作業では、最初に、パレット自動倉庫から搬出された商品をKyoto Roboticsと共同で開発した、ビジョンセンサとAIを備えた「AIケースピッキングロボット」がトータルピッキングする。RDC埼玉ではマスタレス化により事前マスタ登録時の人的ミスやピッキングエラーを低減。ピッキング速度は1時間700ケースの世界最速を実現した。
トータルピッキング後のケース品は「ケースシーケンサー」にて順立てられる。多様な形状のケースを一旦格納し、後工程の「AIケースローディングロボット」で最適な積み付けができるよう順立てした上で、適切なタイミングで出庫する。
AIケースローディングロボットはMujinと共同開発し、ケース品をカゴ車やパレット、カートラックの最適な場所へ自動で積み付ける。積付順は、積載効率のみならず、配送業務を考慮した重量・軽量物の配置や破損を極力防ぐ置き方を計算。処理能力は、こちらも世界最速の1時間当たり450ケースとなっている。
ケース出荷品のうち物流センターなどへの総量納品は人手による作業としている。こうした手作業でも作業者の身体的負担を軽減する仕組みを開発。積み付けの高さを常に作業者の腰位置に維持する装置、ケース積み付けシステム「E‐ELS」を導入している。
積付後のパレットへのフィルムラッピングも自動化し、配送ドライバーの作業負担を低減。ドライバーは出荷バースに到着した荷物をトラックに積み込むだけで庫内作業が完了する。一連のケース品の出荷作業において、フォークリフトは一切使われないという。
AIピースピッキングロボットを日本で初めて導入
バラ出荷品は「ストレージトレーステーション」で商品を正箱から保管トレーに移し替えた上で、トレー自動倉庫にて一時保管される。自動倉庫への格納時には商品とトレーをバーコードでデータと紐づけするとともに「ウェイトチェッカー」で重量検品を行い計数ミスを防ぐ。
トレーに移し替える際に発生する正箱の開封作業には、箱上面を自動でカットする「オートカートンカッター」を開発して運用。同機で対応できない正箱は作業者が開封するが、その際にも、自社開発の手動段ボールカッター「SSカッター」を使えば約4秒でカットできる。
バラ品の出荷作業では、トレー自動倉庫から搬出された商品を「ピックトレーステーション」で「AIピースピッキングロボット」と作業員が必要数量をピックトレーに仕分ける。AIピースピッキングロボットはRightHand Roboticsと共同開発し、吸着機能と指で掴む機能を併せ持つ独自のグリッパ(手)で多様な商品を高速で掴み、置くことが可能。ここでもウェイトチェッカーによる重量検品が行われる。
ピックトレーに仕分けられた商品は「パックエリア」にて「クロスベルトソーター」で店舗別に仕分けられ、店舗向けのオリコンに詰め替えられる。パックエリアでもピックトレーのIDをスキャンする二重検品を行い、誤出荷を徹底的に防止する。
満載になったオリコンはコンベアで搬送され、「オリコンシーケンサー」にてオリコン6個分を順立てし、オリコン自動積付機「オリコンスタッカー」で専用キャリーに積みつけられ、出荷バースへ搬送する。
一連のバラピッキング作業は全体の7割に当たる出荷頻度B、Cランク品が対象で、残り3割のAランク品はカートンのままケース自動倉庫へ格納され、出荷時にはトレー自動倉庫を経ず、「ダイレクトピックステーション」にて直接ピックトレーに仕分けられる。その後はB、C品と同様にパックステーションで店舗別に仕分けられる。
RDC埼玉ではこうした出荷頻度や出荷ロット別に最適な作業工程を組み立てているが、そこで課題となるのが出庫のタイミングだ。ケース品とバラ品、またバラ品の中でも出荷頻度の異なる商品を同一トラックへスムーズに積み込めるよう、「出荷バースに同じタイミングで到着するシステムの構築を重視した」と佐塚氏は話す。
同氏は、RDC埼玉の立ち上げについて「全体をスムーズに流すことと、センター内で働く人の意識改革が重要だった」と振り返る。自動化設備と人手による作業が混在する中、各システムをシームレスにつなげる庫内設計には、先行稼働したRDC新潟の経験が大いに活かされたという。
一方で、RDC新潟は近接する「RDC見附」からの移転・拡充で作業者もそのまま移行できたが、移転前のRDC東京と50㎞以上離れるRDC埼玉は新規採用者がほとんど。登録人数385人のパートスタッフとともに、限られた期間内で大規模センター稼働までこぎつけることには苦慮した。
RDCの常駐社員についても「これまでの人手中心の倉庫と自動化したセンターは運営方法や発想が異なり、その意識の転換が必要」と三木田氏は話す。その上で、「将来的にはセンター長に求められる経験や勘をAIに落とし込み、運営そのものもAI化するのではないか」と展望する。
生産性2・5倍の実現へ製配販の情報連携も提案
RDC埼玉では今後、作業生産性をさらに高める。現在は従来比で2倍を達成しているが、最大2・5倍まで高められる試算にあり、「ちょうど1年が経過してデータが溜まってきたところ。自動倉庫内の格納アルゴリズムひとつ取ってみても、データの分析でさらなる改善が可能」(三木田氏)として実現を目指す。
また、現在はロボットと人がそれぞれ得意な作業を担当しているが、「いずれは全てロボットへ集約したい」と同氏は話す。AIピースピッキングロボットの作業対象商品も徐々に増加しており、自動入荷検品システムも、今は単一SKUのパレットのみが対象だが、複数SKUを積み付けたパレットにも対応できるよう、運用を含めた開発を進める。
その上で、SPAIDを導入した新たなRDCの準備も推進し、既に用地は取得済みだ。
併せて、さらなる自動化に向けた課題として指摘するのが、曜日波動の大きさ。RDCは週6日(月~土)稼働だが、週明けと週末、さらにはチラシ商品の出荷増など物量の波動は激しく、設備や人的配置のムラが生産性を押し下げてしまう。「流通業における永遠の課題」と佐塚氏は話す。
解決に向けては、サプライチェーン上における在庫の可視化と最適化を提案。メーカー・卸・小売の連携と協働により各プレイヤー間で在庫情報を共有し、各工程で最適在庫を常に維持できれば、発注サイクルの定期化や出荷量の平準化が実現し、さらなる自動化システムの導入が可能となる。サプライチェーン全体の工程も最適化できるもので、「積極的な改善提案を進め、業界全体で効率化に取り組んでいきたい」(佐塚氏)という。
(2021年6月29日号)