倉庫にモノづくり機能の一部を移管=タカラスタンダード
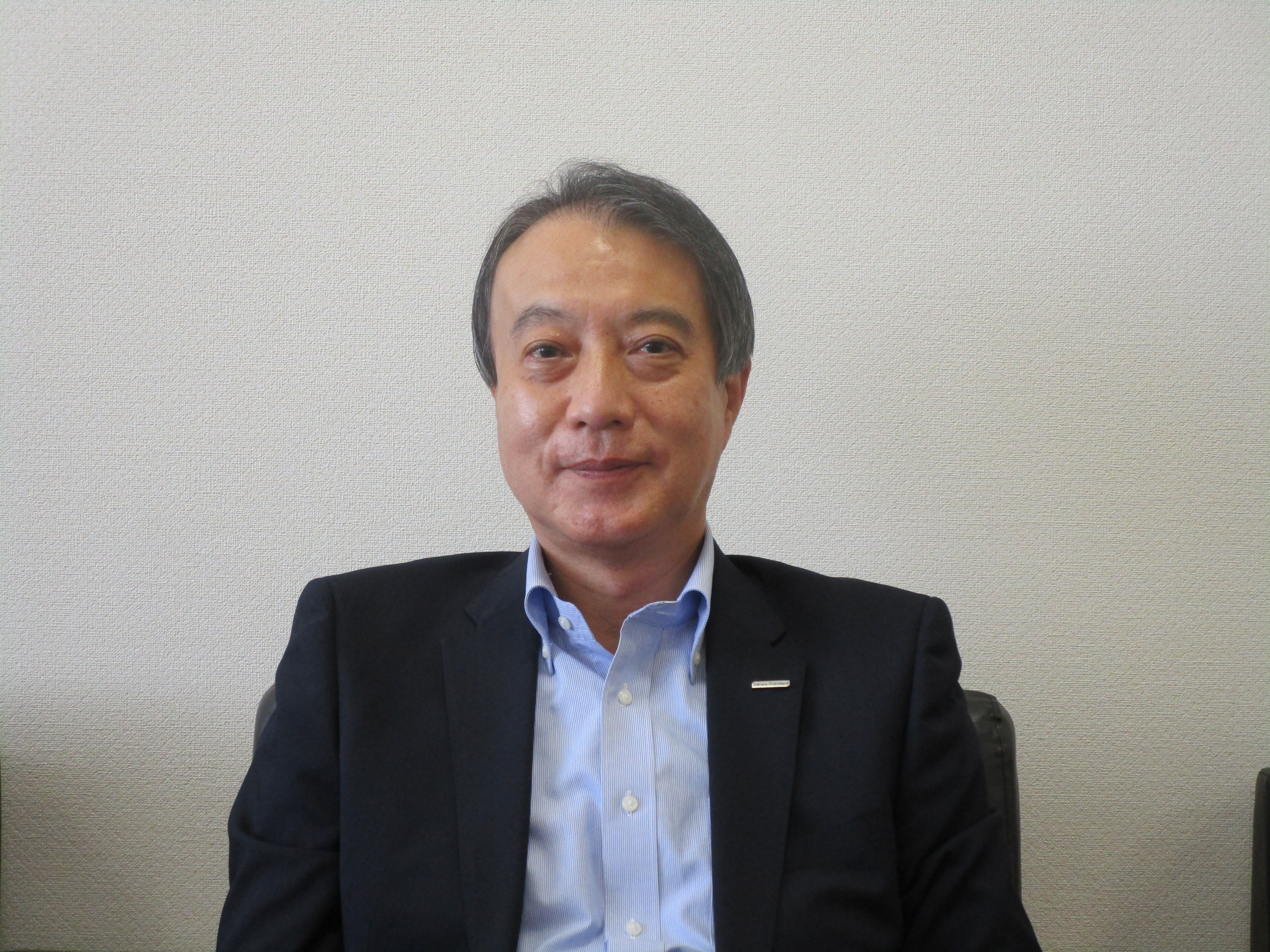
タカラスタンダード(本社・大阪市城東区、渡辺岳夫社長)は、全体最適を目指すサプライチェーン改革を本格化させる。水回り住設機器を効率的に運びやすい半製品の状態で工場から倉庫に移送し、倉庫で製品に組み立て、施工現場へ短納期で出荷する体制を整える。消費地に近い倉庫にモノづくり機能の一部を移管することで、工場の生産効率アップと幹線輸送のコストの削減、リードタイムの短縮を実現する。
サプライチェーンを横串にする組織体制に
同社は2019年4月の組織改正で、本社各本部・各部を再編し、「管理本部」「営業本部」「生産物流本部」「研究開発本部」の4本部体制に移行した。「生産物流本部」は、各工場を統括するとともに、旧生産技術本部を改称した「生産技術部」、旧業務統括本部を改称した「ロジスティクス部」、「購買部」の3つの部を傘下に置き、サプライチェーンを横串にする機能を担う。
鈴木秀俊常務取締役生産物流本部長(写真)は、「ドライバー不足でトラックの確保が難しくなり、物流コストは右肩上がりに上昇している。働き方改革への対応として、工場や倉庫でのトラックの待機時間削減も求められ、物流部門単独による“縦割り”的な改革では限界があった。生産、物流の各部門の部分最適ではなく、全体最適の視点でサプライチェーン改革を進めるための組織に生まれ変わった」と説明する。
倉庫で製品に、幹線輸送コスト削減
サプライチェーン改革では、「運ばない物流」「在庫しない倉庫」「人のいない工場」の3つのテーマを打ち出し、「工場=生産」「倉庫=保管・運搬」という従来の機能を俯瞰的に見直し、資産の有効活用を検討。そこで浮上した案が「倉庫でのモノづくり」で、工場から消費地に近い倉庫に半製品の状態で移送し、そこで製品に組み立てる構想。今年度中に東日本の倉庫でプランを実現し、3年程度で他の拠点にも展開する。
従来は国内にある18の工場で製品としてから5ヵ所の倉庫に移送し、そこから施工現場に届けていたが、引き出しなどを取り付けた製品はかさ高となり「空気を運んでいる」(鈴木常務)。倉庫で製品に組み立てることで、工場から倉庫への移送はユニット化により積載率が向上し、幹線輸送のコストを抑制。工場は顧客ごとの多品種生産から解放され、生産効率を上げられる。また、受注から納期までのリードタイムも短縮する。
在庫削減でスペース捻出、荷捌き場も充実
モノづくりのスペースを捻出するため、納期から逆算して適正なタイミングで生産、倉庫に移送することで在庫を削減。同社の5つの倉庫は平均で延床面積4万㎡強の多層建てで、従来は工場から移送した製品を一度、倉庫に格納し、トラックに積み替えて出荷していたが、“縦持ち”のロスをなくすため荷捌き場での積み替えを推進する。首都圏では自社倉庫近隣に新たに倉庫を賃借し、積み替え用の荷捌き場を充実させる。
倉庫で製品に組み立てる作業については、倉庫の運営を担当している物流会社に委託する予定。工場での作業が減った分、倉庫での作業が増えることになるが、鈴木常務は、「右肩上がりの輸送コスト上昇を抑制するための供給体制をつくるのが最大の目的であり、製品の状態で輸送すると積載効率が悪い機種をターゲットに優先的に取り組んでいく」としている。
(2020年7月16日号)